Dip Moulding 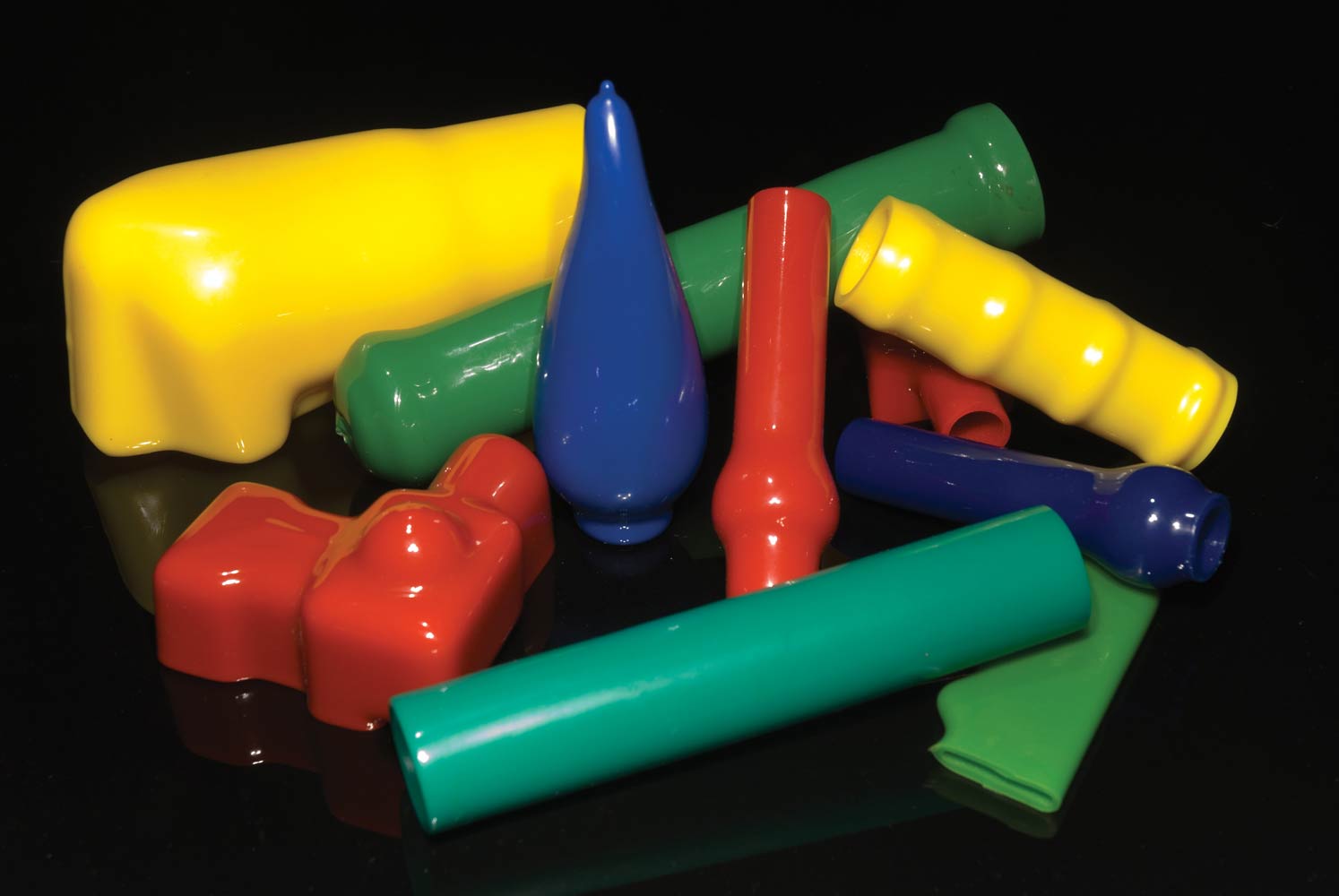
Dip moulding is essentially a technique for the economical production of flexible and semi-rigid PVC components. Often used for mass production. It is particularly suitable for medium and small quantities. more>>
Plastic Casting is a variation of the dipping process generally employed for the manufacture of flat moulding which require a raised or patterned design on one face only. Mouldings such as the model tyre wheel illustrated can be cast with a surface detailed pattern on more than one face. more>>
Slush moulding is a closely related but somewhat different technique to dip moulding and is used for the production of flexible and semi-rigid mouldings where a detailed surface finish is required on the outside of the moulding. more>>
Applications

Agricultural |
|

Medical Applications |
|

Off Road Vehicles |
|

Switchgear |
|
|
|
|
|
|
|

Electrical |
|

Automotive |
|

Mobile Industry |
|

Oil Industry |
|
|
|
|
|
|
|

Civil Engineering |
|

Marine Industry |
|

Material Handling |
|

General Engineering |
Materials used in Dip Moulding
Material performance
PVC plastisol - the principal material used in dip moulding consists of PVC polymer suspended in a plasticiser to which is added stabilisers and pigments.
Tensile strength and elongation at break
Tests were conducted generally in accordance with the appropriate section of BS 2782. Average results were as follows:
Material grade ref. |
Hardness Shore A |
BF softness number |
Specimen temperature MN/m2 |
Maximum stress at break |
Percentage elongation |
PDM100 |
55 |
85 |
23°C |
9.6 |
473 |
PDM100 |
55 |
85 |
65°C |
9.4 |
460 |
PDM102 |
75 |
45 |
23°C |
14.1 |
398 |
PDM102 |
75 |
45 |
65°C |
13.6 |
400 |
|