










|
 |
Material performance
PVC plastisol - the principal material used in dip moulding consists of PVC polymer suspended in a plasticiser to which is added stabilisers and pigments.
Tensile strength and elongation at break
Tests were conducted generally in accordance with the appropriate section of BS 2782. Average results were as follows:
Material grade ref. |
Hardness Shore A |
BF softness number |
Specimen temperature MN/m2 |
Maximum stress at break |
Percentage elongation |
PDM100 |
55 |
85 |
23°C |
9.6 |
473 |
PDM100 |
55 |
85 |
65°C |
9.4 |
460 |
PDM102 |
75 |
45 |
23°C |
14.1 |
398 |
PDM102 |
75 |
45 |
65°C |
13.6 |
400 |
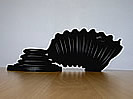
Tear strength
Tests were carried out at 23° C generally in accordance with BS 903.
Average results were as follows:
Material grade ref. |
Hardness Shore A |
BF softness number |
Tear strength |
PDM100 |
55 |
85 |
27.4 |
PDM102 |
75 |
45 |
50.6 |
High temperature performance
Mouldings made from plastisol soften and become more elastic with increasing temperature. We would not recommend the use of mouldings produced from general grades of plastisol at continuous temperatures above 65° C. Specialised grades such as PDM 100 HT are available and there can be used at continuous temperatures up to 90° C, with intermittent use at higher temperatures.

Electrical insulation properties
Tests were carried out in accordance with BS 2782:202A and 203A.
Average results were as follows:
Material grade ref. |
Hardness Shore A |
BF softness number (Ohms) |
Surface resistivity (Ohm centimeter) |
Volume resistivity |
PDM 100 |
55 |
85 |
1.3 x 10 (12) |
5.0 10 (10) |
PDM 102 |
75 |
45 |
1.2 x 10 (12) |
3.3 x 10 (11) |
Chemical resistance
PVC dip mouldings have a generally high splash resistance to a wide range of chemical reagents. We recommend that we are advised of the environment in which the moulding is to be used in order that we can confirm the degree of compatibility and, if necessary, carry out tests.
The following table gives a general guide to the anticipated resistance of mouldings splashed with various chemicals at 20° C:
Resistant |
Some attack |
Acetic acid (60%) |
Hydrogen peroxide |
Nitric acid (70%) |
Ethyl alcohol |
Hydrogen peroxide |
Sulphuric acid (80%) |
Calcium hydroxide |
Nitric acid (50%) |
Degraded |
Detergents |
Phosphoric acid (30%) |
Acetone |
Glycerine |
Sea water |
Carbon tetrachloride |
Hydrobromic acid |
Sodium hydroxide |
Benzene |
Hydrochloric acid |
Sulphuric acid (50%) |
Petrol |
Hydrofluoric acid |
Transformer oil |
Trichloroethylene |
Material selection
We manufacture our own PVC plastisols and have developed a large range to suit widely differing requirements. Developments of new grades continues and, if necessary, we can enhance a particular property of a small grade.
Most grades are available in black, white and a wide range of colours. Some colours are offered as standard whilst other can be matched as required. Although many grades have a high gloss, opaque finish, some can be matt, textured, or alternatively translucent.
Your logos or other details such as operating instructions can be printed on most mouldings using highly tenacious inks.
Flame retardancy
Additives can be incorporated in all our plastisols,
except food grades, to improve their resistance to flame. The specialised grades listed above include PDM 100 FR spec. UL.94-VO ).
Toxicity
Most of our plastisols are classed as non toxic. It is not possible to list the complete range of materials that can be manufacture, please consult us for further information.
Electrical covers & boots – Dip Moulding
MATERIAL |
GRADE REFERENCE |
HARDNESS SHORE A |
BS SOFTNESS NUMBER |
COLOUR AVAILABILITY |
FINISH |
TYPICAL APPLICATIONS |
Plasticised PVC- General Grades |
PDM 100 |
55 |
85 |
Black, white, colours |
Glossy or matt |
General purpose flexible material. Uses include bellows and electrical insulating shrouds. Good low temperature properties |
PDM 101 |
65 |
65 |
Black, white, colours |
Glossy or matt |
Slightly stiffer material ideal for complicated ducting |
PDM 102 |
75 |
45 |
Black, white, colours |
Glossy or matt |
Most suitable for grips, end caps and sleeves |
PDM 103 |
85 |
35 |
Black, white, colours |
Glossy or matt |
Stiffer grade – used for boxes and covers |
PDM 104 |
45 |
100 |
Black, white, colours |
Glossy |
Most flexible grade available – ideal for protective boots. Good low temperatures properties. |
PDM 109 |
95 |
15 |
Black, limited colours |
Semi-gloss |
Stiffest grade available – used for pipe bends and instruments covers |
Plasticised PVC – Specialised grades |
PDM 100 FR Spec UL 94-VO |
55 |
85 |
Black only |
Glossy |
Flame retardant grade of PDM 100
Underwriters Laboratories Inc. – yellow card certification |
PDM 100 FR |
55 |
85 |
White colours |
Glossy or matt |
Flame retardant grade of PDM 100 |
PDM 100 OR |
55 |
85 |
Black, white, colours |
Glossy |
Oil retardant grade of PDM 100 |
PDM 100 HT |
55 |
85 |
Black, white, colours |
Glossy |
Continuous high temperature resistant grade of PDM 100 up to 90°C |
PDM 101 FR |
65 |
65 |
Black, white, colours |
Glossy or matt |
Flame retardant grade of PDM 101 |
PDM 101 OR |
65 |
65 |
Black, white, colours |
Glossy |
Oil retardant grade of PDM 101 |
PDM 102 FR |
75 |
45 |
Black, white, colours |
Glossy or matt |
Flame retardant grade of PDM 102 |
PDM 102 OR |
75 |
45 |
Black, white, colours |
Glossy |
Oil retardant grade of PDM 1021 |
PDM 107 |
55 |
85 |
White & translucent (coloured & clear) |
Glossy |
Flexible grade for foodstuff or medical applications |
PDM 108 |
75 |
45 |
Black, limited colours |
Glossy |
As PDM 107 but for semi-rigid mouldings |
|